-
A.
Capacity is the volume of material your rotary valve can handle per rotation. The calculation involves the rate of conveying, material bulk density, valve efficiency, and RPM of your rotor. We can help you with the math, but if you're just looking for a valve sizing recommendation, you can use our handy calculator tool.
Relevant for: Conveying Systems, Technical Support -
A.
It depends! Do you want a valve with an easy-to-clean design? A valve with multiple ports for split conveying lines? Maybe a valve for heavy-duty applications, for corrosive material, or for metering small batches?
We could go on, but the best way to determine which valve you need is to speak with an ACS Valves rep. Give us the details and we’ll help you choose a rotary valve that’s optimized for your needs.
Relevant for: Conveying Systems -
A.
Because rotary valves come in so many different types and sizes, we don’t list prices online. Please contact an ACS Valves rep to request a quote. We’re happy to walk you through exactly what you need and why.
Relevant for: Conveying Systems -
A.
There are so many! Our standard CI Series valve is popular with its efficient construction and plenty of customization options. But there are dozens of other options, and they depend on:
1. Your application (e.g., construction, pet food, or cannabis processing?)
2. Your material (e.g., cement, plastic, or flour?)
3. Your system (bulk material, dust collector, or pneumatic conveyor?)
4. Your desired valve type (airlock with metering, metering/feeding, or airlock?)You could go even further down the rabbit hole and customize valves with different rotors, coatings, and accessories for maximum efficiency. The easiest approach is to contact an ACS Valves rep to discuss your options — we’ll only recommend what your process actually needs.
Relevant for: Conveying Systems -
A.
A valve is a transfer point in your material handling system, moving bulk solids from containers (think bins, hoppers, and silos) to the conveyor below. It may also move material from one container to another.
Valves can be used to provide a pressurized seal between those points, help control the flow of material, or both. Basically, they help you move material efficiently and safely, preventing product loss.
Relevant for: Conveying Systems, Manufacturing -
A.
This is a great question because they’re also called airlocks (or rotary airlock valves, or rotary airlock feeders) — just to make it extra confusing. The catch-all term is rotary valve, which is what we use most often.
The exact term changes depending on how the valve is used. Anything with the word “airlock” in the name is used to maintain a pressure differential between two separate compartments. Feeders are more about controlling the rate of material flow from one place to the next. If a valve does both, you would call it a rotary airlock feeder.
At ACS Valves, we have a lot of multifunctional rotary valves that can serve any of these roles, as well as more specialized valves for airlock or feeding/metering purposes. If you’re not sure what you need, give us a call and we’ll help you figure it out!
Relevant for: Conveying Systems -
A.
That depends on you. Do you need to control the rate of material flow (feeder), maintain a pressure differential between compartments (airlock), or a combo of both (airlock feeder)?
Not sure? That’s okay — give us some details about your process needs, and we’ll make a recommendation.
Relevant for: Conveying Systems -
A.
Sometimes the rotation of the rotor is reduced due to an overload of material, or larger pieces of material being fed through the valve, jamming in the clearances. In this case, shear pin sprockets will shear the pin on the sprocket, reducing the risk of damage to the rotor.
-
A.
Too much clearance between the rotor, endplates and or housing can result in air loss. Measure the rotor to endplate and rotor to housing clearances to confirm that they are an NFPA compliant 0.0079 inches. If the clearance is larger than this, it might be time to replace your rotor, rotary valve, or have it sent back to ACS for a repair or evaluation. Make sure to stick to a maintenance schedule and check your clearances at least every three months.
-
A.
The capped pipe is called a housing vent port. Rotor pockets can sometimes contain a volume of pressured air, which can impede material flow into the airlock inlet, reducing your efficiency. Also, in conveying systems that run at 6 PSI and higher, large releases of air up the return side of the airlock can cause pulsing in the material flow into the conveying line. Using a vent helps solve both of these issues, and is also helpful in improving your fill efficiency.
-
A.
Shear protectors reduce the flow of material at the valve's inlet. Reduced flow allows for better pocket fill and also reduces the risk of product jams in your housing clearances–ultimately protecting your product from damage.
Frequently Asked Questions
Questions about rotary valve manufacturing, troubleshooting, compliance, and more
The rotary valve geniuses at ACS Valves love to help manufacturers with their conveying queries, conundrums, and challenges. Browse our collection of questions and answers here.

Go ahead, make your valve
Put your own spin on our customizable valves to get the best valve for your application, material and industry.

We have a series of items available for quick shipment
Items include: Pressure blower packages, MD Series, S-Pellet Series, Diverter Valves, Flex Tip Series, Screw Conveyors
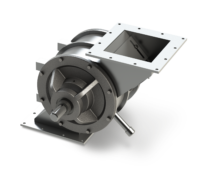
How to: Check rotor-to-housing tolerances
Keep your rotary airlock valve compliant with NFPA guidelines and maintain strong performance by checking your rotor-to-housing clearances regularly.
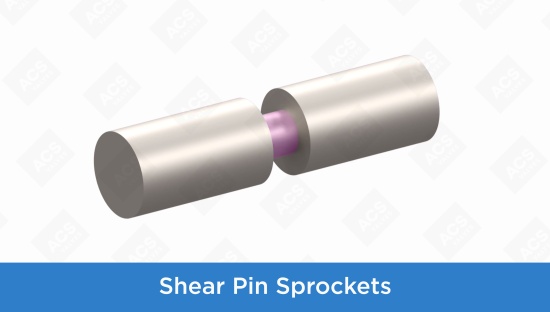
Newsletter
Stay informed on all things ACSWe’ll keep you up-to-date on the latest valve how-tos, handy tips, and news from ACS. It’s totally free and you can opt out at any time.